In the Greek myth of Icarus, wings that melt in the sun are a tragedy. For the U.S. military, however, flying vehicles that vaporize in sunlight could be a potent weapon: picture a drone that vanishes without a trace after covertly delivering supplies to a remote location.
Engineers at the Georgia Institute of Technology have developed a new type of plastic that can form flexible sheets and tough mechanical parts—then disappear in minutes to hours when hit by ultraviolet light or temperatures above 176 degrees Fahrenheit. Previous efforts to make plastics that self-destruct on command have had trouble preventing such materials from disintegrating at room temperature. But the Georgia Tech team’s new substance can remain stable for years, as long as it shuns the sun.
These plastics could also be used to make environmental and medical sensors that dissolve after collecting data or temporary adhesives that come unstuck with the aid of a heat gun. “They are great for applications where you want things to disappear right away,” says Paul Kohl, a chemical and biomolecular engineering professor at Georgia Tech, who presented his team’s latest research on Monday at the American Chemical Society’s national meeting in San Diego.
On supporting science journalism
If you're enjoying this article, consider supporting our award-winning journalism by subscribing. By purchasing a subscription you are helping to ensure the future of impactful stories about the discoveries and ideas shaping our world today.
Kohl’s presentation covered the most recent improvement that Georgia Tech scientists have made to their material, but his team has been working on the formula for years—and it is not the only one trying to craft temporary plastics. The Defense Advanced Research Projects Agency (DARPA) has an entire program—dubbed Inbound, Controlled, Air-Releasable, Unrecoverable Systems, or ICARUS—to fund research that could lead to the development of disappearing air-delivery vehicles, including Georgia Tech’s work.
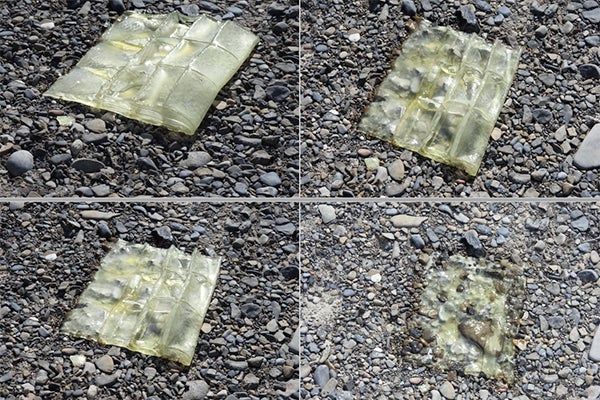
A glider wing made from the polymer dissolves in sunlight. Credit: Paul Kohl
The task is daunting. Plastic consists of synthetic polymers, long chains of smaller molecules linked with superstrong bonds. Reverting them to their building blocks requires breaking each bond, akin to ripping apart a necklace bead by bead. Because this process can be affected by humidity, acidity, temperature and other factors in a material’s environment, the breakdown can take months—if it happens at all. “There are many synthetic plastics that kind of degrade,” Kohl says, “but it’s a slow and painful process.”
To make durable plastics that quickly destruct on command, Kohl’s team and some other researchers have turned to a molecule called poly(phthalaldehyde) (PPHA). Like all polymers, this one splits up into its building blocks when heated above a certain temperature. But in contrast to the plastics used in bottles and packaging, which only break down at very high heat, PPHA unravels while still below room temperature. This property makes it easy to break down but hard to stabilize.
To trick PPHA into being pseudo stable, Kohl and his colleagues linked the chain into a circle. “It only depolymerizes from the end inward,” Kohl says. With its tips linked together, the chain does not break down as easily. “It’s like peeling a banana,” Kohl explains. “It’s hard to peel from the middle.” Although the circle structure keeps the modified PPHA from breaking down at a typical room temperature, if a trigger snips just one bond, “the whole thing instantly depolymerizes and completely falls apart,” he says.
“It’s pretty clever, the way they have designed the polymer to unzip from that one bond breaking,” says Andrew Dove, a professor of chemistry at the University of Birmingham in England, who was not involved in the new research. The Georgia Tech team further fine-tuned the unzipping process by adding a soup of chemicals to the circular PPHA. In order to trigger the polymer’s undoing on command, the researchers mixed in a compound that becomes acidic in the presence of sunlight and then attacks PPHA bonds. And to slow down the speed of this degradation—thus giving a simple flying machine such as a glider enough time to complete its mission—they added additional compounds that react with and weaken the acid.
Even in its circular form, though, the PPHA was initially not quite stable enough for a long haul. Kohl and his colleagues discovered that impurities in the polymer—mainly traces of the catalyst boron trifluoride, which is used to assemble PPHA chains—were the main culprit. By removing all such impurities, they have boosted the material’s shelf life. “It should last for 20 years indoors, at room temperature,” Kohl says. “Fluorescent light does not bother it.”
Despite these improvements, the resulting plastic was hard to use because of its relatively brittle texture. But at the American Chemical Society meeting, Kohl announced that he and his colleagues have fixed that problem by adding ionic liquids—salts in liquid form—to the plastic. Doing so alters its mechanical properties in different ways: one type of ionic liquid makes the plastic tough and hard, perfect for glider wings, while another renders it soft and foldable for other uses, Kohl says.
DARPA has already used the plastic to make light, strong gliders and parachutes. Last October the agency field-tested one of these vehicles: dropped from a high-altitude balloon at night, a glider successfully delivered a three-pound package to a spot 100 miles away. After four hours in the sun, it vanished, leaving behind nothing but an oily smudge on the ground. Kohl says the plastic could dissolve even faster under a glaring midday sun, in some cases taking as little as five minutes.
The new plastic still faces challenges. For example, Dove emphasizes that the light-triggered degradation will limit its uses. “It’s a great idea,” he says, “but I’m not sure it’s going to translate into consumer plastics.” What’s left behind when the plastic disintegrates also matters. Nothing disappears completely, points out Ann-Christine Albertsson, a chemist at the KTH Royal Institute of Technology in Sweden. “The degradation products and how they interfere with the environment are important,” she says.
In this case, the leftover products—that oily smudge that was once the test glider—primarily consist of the ionic liquids with which the researchers treated the polymer. These substances are antimicrobial chemicals, similar to ones “used in hospitals in antibacterial wipes,” Kohl says. “However, they would not be appropriate for human consumption or touching food products. In the future, we will try to change them to [be] vaporizable.”